基本的な考え方
人口増加や新興国の経済成長などにより、鉱物や化石燃料をはじめとする資源の消費量が増加しています。
三菱自動車グループは、より少ない資源を投入し、効率的に利用して自動車を製造することが自動車の価値の向上につながるとの考えにもとづき、資源の有効利用を重要な課題と捉えています。「環境計画パッケージ」では資源循環を当社グループが直接的に取り組む環境課題の一つと位置付けており、資源循環型社会の実現への貢献を目指し、投入資源の最小化と資源効率の最大化に向けた取り組みを推進しています。
当社は、国や業界団体が自動車のリサイクルと適正処理を促進するために策定したイニシアティブを受け、1998年に「三菱自動車リサイクルイニシアティブ」を策定し、リサイクル可能率の向上、鉛の使用量削減、新型車へのリサイクル材の適用に関する目標を定め、継続的に取り組んでいます。
リサイクルに配慮した設計・開発
日本、欧州、中国をはじめ各国では、自動車リサイクルに関する法制化が進み、リサイクルに配慮した製品開発が自動車メーカーに求められています。
当社は、リサイクルだけでなく、リデュース、リユースの3Rを積極的に取り入れた設計・開発を進めています。
また、リサイクル材やバイオマスプラスチックをはじめとする脱石油資源プラスチック材の採用拡大を推進しており、衣類などを回収・リサイクルした古衣料リサイクル材をダッシュボードといったサイレンサー部品に、バイオマスプラスチックをステアリングホイールガーニッシュなどの内装部品に採用しています。
さらに、販売会社で修理時に生じる廃バンパーを回収・再生して、バッテリートレイなどの外装部品に採用しています。引き続き脱石油資源プラスチック材の採用を拡大するため、開発を進めていく予定です。
TOPICS
熱可塑性樹脂の採用
2024年に販売した『エクスフォース』(HEVモデル)は、外装及び内装にリサイクルが容易な「熱可塑性樹脂(※1)」を採用しています。
- 熱可塑性樹脂:常温では変形しにくいが、加熱すると軟化して成形しやすくなり、冷やすと再び固くなる性質を持つプラスチック。
熱可塑性樹脂の主な採用箇所(グリーン部)
-
外装
-
内装
使用済自動車のリサイクル促進
当社グループは、使用済自動車の廃棄物が環境に与える影響を低減するため、使用済自動車のリサイクルを推進しています。日本やEUなどでは、各国の自動車リサイクル法にもとづいてリサイクルを促進し、今後、アジアの新興国においても制定の動きがある自動車リサイクル法にも確実に対応していきます。
また、「環境ターゲット2030」において、取り組むべき事項の一つに電動車の使用済みバッテリーの再利用を掲げており、省資源の観点から、使用済みバッテリーの活用に向け取り組んでいます。
電動車の使用済みバッテリーの再利用
電動車の使用済みバッテリーのなかには、他の用途であれば十分に活用できる充電容量を残しているものがあり、省資源の観点から、使用済みバッテリーの有効活用が電動車の課題の一つとなっています。当社では、蓄電用途での活用の可能性を確認するため、岡崎製作所に大規模太陽光発電設備と併せて、『アウトランダーPHEV』(旧モデル)の使用済みバッテリーを活用した蓄電システムを設置し、実証を行っています。
また、電動車用の急速充電器および双方向充電器と連携する2つのコンセプトの実証設備を2023年1月に岡崎製作所に設置し、実証試験を行っています。将来的には蓄電設備メーカーと連携して、当社グループの販売会社の店舗などへの導入をめざしていきます。
さらに、当社とMIRAI-LABO株式会社は、電動車の使用済みバッテリーを用いた自律型街路灯の開発を進めてきました。自律型街路灯は、日中に太陽光で発電した電力を電動車の使用済みバッテリーに蓄電し、夜間はその電力でLED照明を点灯させるものです。当社は2022~2023年度に岡崎製作所、水島製作所、京都製作所、十勝研究所の所内に計24基の自律型街路灯を設置して実証実験を行い、さらに2025年3月には自律型街路灯の販売を開始し、1号基を岡崎市社会福祉協議会サービスセンターに設置しました。
これらに加え、当社グループは、日本、欧州、北米において、電気自動車やプラグインハイブリッド車(PHEV)の使用済みバッテリーのリサイクル技術開発・適正処理を目的として、使用済みバッテリーの回収体制を構築し運用しています。
国内自動車リサイクル法への対応
国内では、2005年に施行された自動車リサイクル法にもとづき、使用済みとなった自動車のシュレッダーダスト(ASR(※2))、エアバッグ類、フロン類の3品目を引き取り、再資源化を行っています。
ASRのリサイクルは、ART(※3)に参画し、ASRを共同処理しています。新規処理施設の開拓などにより、2024年度のASR再資源化率は96.7%で、2015年以降の法定基準70%を大幅に上回りました。引き続き、安定的にASRがリサイクルできるように新規リサイクル施設の開拓を推進します。
エアバッグ類・フロン類は、一般社団法人自動車再資源化協力機構に処理業務を委託しています。
なお、2024年度の使用済自動車リサイクル実効率(※4)は99%以上に相当し、政府の定めたリサイクル実効率95%を上回っています。
- ASR:Automobile Shredder Residueの略称。自動車破砕残さ
- ART:Automobile shredder residue Recycling promotion Teamの略称。日産自動車株式会社、マツダ株式会社、当社など12社で設立した自動車破砕残さリサイクル促進チーム
- リサイクル実効率:使用済自動車のリサイクル率。解体・シュレッダー工程で再資源化された比率約83%(2003年5月中央環境審議会 自動車リサイクル専門委員会と産業構造審議会自動車リサイクル WGの第3回合同会議資料より引用)に、残りのASR率17%と該当年度のASR再資源化率を乗算したものを加算して算出した。
EUでのリサイクル促進
EU自動車リサイクル法への対応
EUでは、2000年に発行されたELV指令(※5)にもとづき、自動車メーカー又は輸入業者に使用済自動車の引き取り・リサイクルが義務付けられています。
当社グループは、欧州の現地法人であるミツビシ・モーターズ・ヨーロッパ・ビー・ブイ(MME)を中心に、EU加盟国の実情に合わせた引き取り・リサイクルの体制を構築しています。
- ELV指令:使用済自動車に関する欧州議会及び閣僚理事会指令
解体情報の提供
EUでは、新型車の解体情報を解体業者に提供することが義務付けられているため、当社は自動車メーカーが共同で設立した解体情報システム「IDIS(※7)」を利用して、タイムリーに情報を提供しています。
- IDIS:International Dismantling Information System
EUリサイクル可能率認証指令への対応
EUでは、リサイクル可能率95%以上を達成することが自動車の型式認証要件となっており、当社グループは本指令の要求事項に適合させる体制を構築しています。当社グループがEUで販売する車両は、この体制のもと本指令の要求事項に適合させています。
生産活動における排出物の発生抑制と再資源化の取り組み
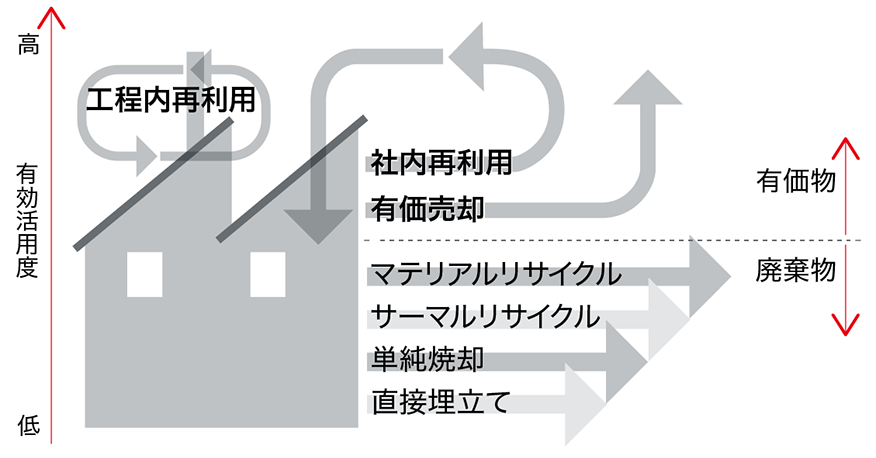
資源の有効活用/リサイクルのイメージ
生産工場では、工程の改善などを通じて、生産過程における廃棄物など排出物の発生抑制に取り組んでいます。また、発生した廃棄物などについては、処理コストを抑制しつつ、資源としてより有効活用されるよう、分別方法や処理方法を継続的に改善しています。
プラスチック資源循環促進法に関する対応
当社は2024年度にプラスチック使用製品産業廃棄物等(以下、廃プラ)の再資源化率100%を達成しました。今後も廃プラのリサイクルを推進し、再資源化率100%(※8)を継続します。
プラスチック使用製品産業廃棄物などの排出量・再資源化率
(岡崎製作所、水島製作所、京都製作所)
2023年度 | 2024年度 | |
---|---|---|
排出量 | 1,796t | 1,973t |
再資源化率 | 97% | 100% |
- 再資源化率は、一般社団法人日本自動車工業会の再資源化率の算出方法に基づいて計算
TOPICS
汚泥脱水装置の更新による廃棄物量の低減(岡崎製作所)
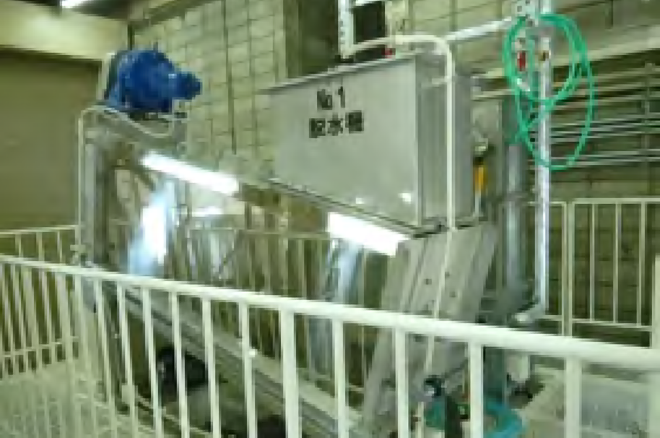
スクリュー式汚泥脱水装置
岡崎製作所では、総合排水処理場にある汚泥脱水機・汚泥搬送装置の更新に合わせ、従来とは異なる処理方式を採用した装置に変更し、産業廃棄物の排出量を低減しつつ、省エネ化しました。
これまでは汚泥の脱水に遠心分離方式を用いていましたが、より汚泥の含水率を下げるため、スクリュー式の脱水機を採用し、汚泥の搬送方式も省エネタイプに変更しました。これらの設備更新により、総合排水処理施設から排出される汚泥を従来よりも30%以上低減しつつ、電力使用量についても50%以上低減しました。
直接埋立廃棄物のゼロ化
事業活動から発生する廃棄物について、「環境ターゲット 2030」で掲げる「直接埋立廃棄物のゼロ化(0.5%未満)」に向け、社外排出量の低減、再資源化を推進しています。
2024年度は環境マネジメント対象会社において、直接埋立廃棄物ゼロ化(0.5%未満)を達成しました。