Basic Approach
Vehicles are products that can affect human health and biodiversity through the emission of environmental pollutants and chemical substances during business activities or product use.
MITSUBISHI MOTORS Group aims to contribute to the realization of a pollution-free society and has positioned this as one of the key challenges in its Environmental Plan Package. We are working to reduce the environmental impact of our products and the pollution resulting from our business activities. In the stage of product development, along with reducing noxious components of exhaust gases and promoting the development of fuel economy improving technologies and electrification technologies, we strive to manage hazardous substances. In production processes, we are endeavoring to reduce air pollutants emitted from out plants by voluntarily enacting activity standards that are stricter than legal requirements.
Throughout all of our business activities, we are carrying out initiatives aimed at reducing the impact on the environment from chemical substances.
Purifying Exhaust Gas while Driving
In addition to developing and popularizing electrified vehicles, which emit little exhaust while driving, we are endeavoring to develop and improve gasoline and diesel vehicles that emit fewer hazardous substances.
Improving Gasoline Engine Vehicles
In the 1960s, emissions of carbon monoxide (CO), hydrocarbons (HC) and nitrogen oxides (NOx) were restricted by regulations, and those restrictions have gradually been tightened since.
We have taken various measures since such regulations were first introduced. Currently, our products are compliant with strict emission regulations, thanks to the advanced technologies such as electronically controlled fuel injectors for combustion control, gasoline particulate filter (GPF) systems, and improved catalyst technologies.
Improving Diesel Engine Vehicles
For diesel engine vehicles, emissions of CO, HC, NOx, and particulate matter (PM) *1 have been regulated in some countries and regions, such as Japan, United States and European countries, since the 1970s.
Since such regulations were first introduced, we have taken measures including improving the combustion technology. To comply with these regulations, we have developed and produced clean diesel engines by systemizing combustion control technologies such as variable geometry turbocharger and high pressure fuel injection system, as well as after-treatment technologies such as NOx trap catalyst, diesel particulate filter, and urea selective catalytic reduction system.
- Micron-sized particles such as soot contained in exhaust gas
Clean Diesel Engine Systems
Variable Geometry (VG) Turbocharger
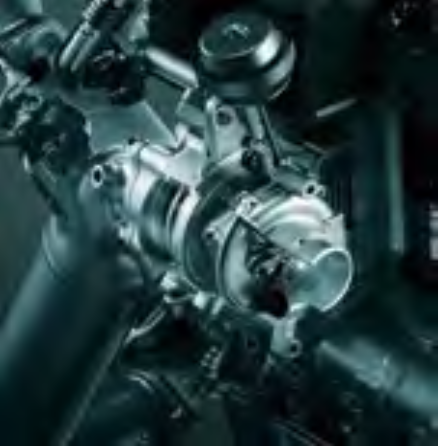
Continuously controlling the variable nozzle of the turbine optimally boosts power to the engine throughout its full operating range, improving fuel efficiency and reducing PM emissions.
Common Rail Fuel Injection System
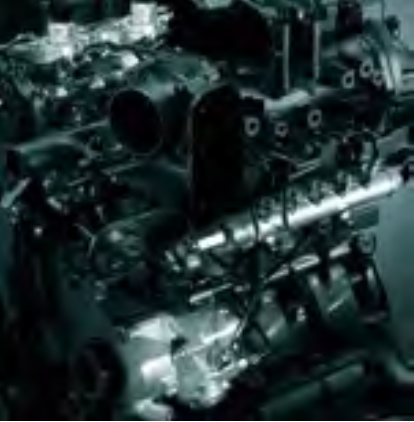
Particulate matter and NOx, which can be generated through heterogeneous combustion, are suppressed by using a high-pressure fuel pump, common rail accumulator that stores highly pressurized fuel, and electronically controlled fuel injectors.
Diesel Particulate Filter (DPF)
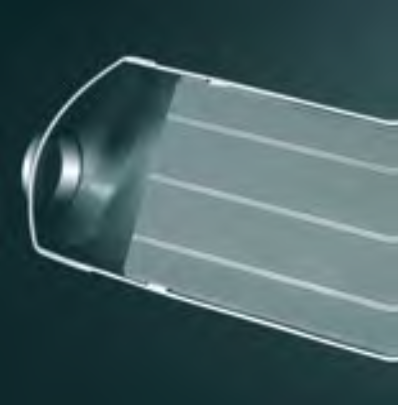
DPF substantially reduces emissions of particulate matter by filtering and burning it.
Urea Selective Catalyst Reduction (SCR) System
NOx from diesel engines’ emissions are reduced and purified using an aqueous urea solution (AdBlue®*2), breaking them down into non-polluting nitrogen and water.
- Registered trademark of the Verband der Automobilindustrie (VDA)
[Clean Diesel Engine System (4N14 Engine)]
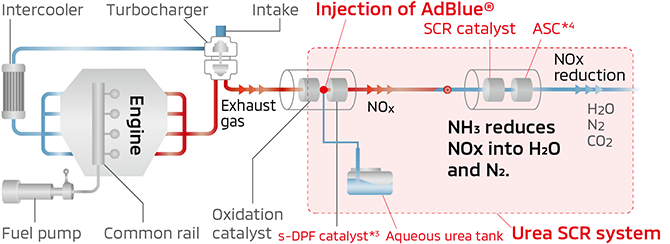
- s-DPF: DPF with surface-coated selective reduction catalyst
- ASC: Ammonia slip catalyst
Reduction of Hazardous Substances
In accordance with the reduction targets of the Japan Automobile Manufacturers Association, Inc. (JAMA) and the EU’s end-of-life vehicles directive (a recycling law), MITSUBISHI MOTORS Group is working to reduce the use of four substances (lead, mercury, cadmium, and hexavalent chromium). We are also taking measures to comply with individual countries’ regulations on the use of hazardous substances, such as the EU’s end-of-life vehicles directive, the REACH regulation*5 concerning substances and the Convention on POPs*6.
At present, in addition to four substances and other heavy metals, the use of VOCs*7, bromine-based flame retardants and various other substances is regulated. Regulations similar to European ones are being enforced in developing countries in Asia as well.
The Group is working to voluntarily reduce hazardous substances by setting internal technical standards.
- REACH stands for “Registration, Evaluation, Authorisation and Restriction of Chemicals.” Enacted on June 1, 2007, the REACH regulation is a general system to register, evaluate, authorize and restrict the use of substances
- Persistent Organic Pollutants
- Volatile Organic Compounds
Management of Material Data by IMDS
To manage and reduce the amount of hazardous substances contained in vehicle parts delivered by suppliers, data regarding these substances are collected by the IMDS*8, an international system for collecting such data. Together with overseas, we utilize the collected data under a globally centralized internal system for reducing hazardous substances.
We ask business partners to disclose data on environmentally hazardous substances for materials and parts by inputting them into IMDS in accordance with the “Green Procurement Guidelines.” We also ask them to establish a management system for environmentally hazardous substances. In cooperation with suppliers, we are complying with the REACH regulation, a general system for the registration, evaluation, authorization, and restriction of substances used in the EU.
We reflect updates to information on GADSL-regulated substances in our internal management system to properly manage hazardous substances in products. We collect IMDS data inputted by suppliers and utilize the system to automatically determine the compliance status with regulations if any newly regulated substances are found in components, based on the content and materials used. We are also introducing component replacement and design changes in accordance with regulations.
- International Material Data System

Reduction of In-Cabin VOCs
VOCs are organic compounds that are easily volatilized at room temperature such as formaldehyde and toluene. These compounds are thought to cause sick building syndrome, and may irritate the eyes, nose, and throat. In an automobile cabin, they are mainly generated by adhesives and paint used in interior parts.
In addition to implementing reduction measures for VOC sources, we also take advance measures to respond to VOC regulations, not only those of JAMA but also of future European regulations. We strive to provide customers with healthy and safe cabin spaces.
Please see the JAMA website for details regarding the Voluntary Guidelines for Reducing Vehicle Cabin VOC Concentration Levels.
Preventing Air Pollution
Reduction of VOC Emissions from Production Processes
TO reduce VOC emissions, the Group is applying the waterborne 3WET paint method*9 to the painting process . In Japan, we use this method at the Mizushima Plant and the Okazaki Plant. Overseas, the system is used in two painting plants in Mitsubishi Motors (Thailand) Co., Ltd. (MMTh).
We are also upgrading our robotic and other painting systems, reducing the amount of paint used by adjusting production lots and collecting more used thinner. Through these moves, we are reducing VOC emissions from vehicle production.
- With this method, water-soluble paints are used for the middle and top coats. Solvent-based paint is used only for the clear overcoat.
Management of Air Pollutants
The Group follows laws and regulations to manage the concentrations and amounts of such air pollutants as nitrogen oxides (NOx), sulfur oxides (SOx) and soot emitted in production processes.
In addition, to simultaneously reduce air pollutants and CO2 emissions, we are promoting the replacement of equipment that uses fossil fuels such as kerosene with electric devices, including electric heat pumps.
Management of Chemical Substances
Appropriate Management of Chemical Substances
The Group has introduced a chemical substance management system. Before deploying substances, we examine their physical and chemical properties and the details of usage plans, as well as legal requirements. And we conduct risk assessments, judge whether the substances can be introduced and educate workers thoroughly. We also centrally manage the most recent Safety Data Sheet (SDS) information.
In addition, we use data from this system to ascertain the quantity of PRTR*10 substances used and report on their usage and emissions to Ministry of Economy, Trade and Industry, as well as other aspects of legal compliance.
We will continue to appropriately manage chemical substances from the perspectives of ensuring occupational health and safety and preventing environmental pollution.
- PRTR: Pollutant Release and Transfer Register
Appropriate Management of Hazardous Waste
The Group manages hazardous waste to avoid importing or exporting hazardous waste that is restricted by the Basel Convention on the Control of Transboundary Movements of Hazardous and Their Disposal*11.
We also transport and treat waste produced in Japan appropriately, based on various legal requirements.
- This convention stipulates international frameworks and procedures related to restrictions on international transfer of a certain types of waste.
Appropriate Management of Waste Containing PCBs
Harmful polychlorinated biphenyls (PCBs) are contained as insulation oil in transformers and condensers that were manufactured a long time ago. Our Group processes waste containing PCBs appropriately, in accordance with the Act on Special Measures concerning Promotion of Proper Treatment of PCB Waste.