Governance
Basic Approach
We recognize that addressing the globally shared challenge of achieving carbon neutrality by 2050 is a critically important initiative that will determine the future of the MITSUBISHI MOTORS Group. The Group positions climate change countermeasures as one of the key issues in formulating its business strategies. By incorporating measures to address climate-related risks and opportunities into the Environmental Plan Package, which sets forth the direction and goals of our environmental initiatives, and reflecting them in our business strategies, we are working to ensure sustainable business growth, reduce future risks, and enhance our resilience as a company.
Management Structure
a. Board’s oversight of climate-related risks and opportunities
The Group recognizes “responding to climate change and energy issues” as an important management issue and has accordingly identified it as one of our materiality issues. The Board of Directors makes decisions on important matters related to environmental initiatives, including those related to climate change, and oversees their execution. The Board of Directors approved the “Environmental Vision 2050” and “Environmental Targets 2030,” which were revised in FY2022, and these measures were announced.
Examples of climate change-related issues discussed or reported by the Board of Directors
- Endorsement of TCFD recommendations
- Disclosure in line with TCFD recommendations
- Declaration of intent to achieve carbon neutrality by 2050 and revision of Environmental Vision 2050
- Revision of Environmental Targets 2030
b. Management’s role in assessing and managing climaterelated
To address climate change and energy issues, we have established the Sustainability Committee, chaired by the Representative Executive Officer, president & CEO, who also holds top responsibility for initiatives related to climate change. The committee evaluates climate-related risks and opportunities, discusses response measures, and reviews progress and achievements in line with the Environmental Targets 2030.
We have established the Carbon Neutrality Council under the Sustainability Committee. This council is chaired by the Representative Executive Officer, Executive Vice President and consists of executives responsible for management strategy, products, manufacturing, procurement and logistics. This organization formulates medium- to long-term policies and goals based on the assessment of climate-related risks and opportunities, considering specific response measures in each area. These policies, goals, and their progresses are reported by the respective heads of each area at the Sustainability Committee for review and deliberation. The organization generally meets three times per year, and particularly important matters are deliberated and decided by the Board of Directors.
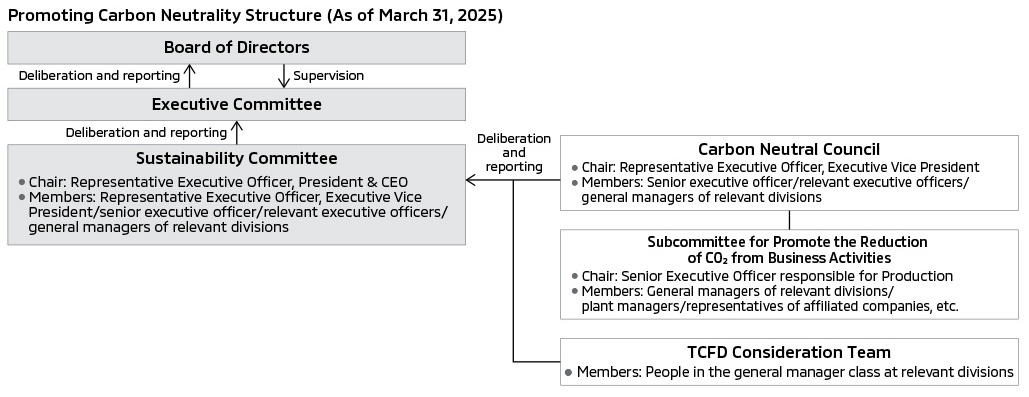
Roles | Meeting frequency | |
---|---|---|
Sustainability Committee | Monitoring Progress toward the Environmental Targets 2030 | Three times a year |
Carbon Neutral Council | Formulating medium- to long-term policies and targets for achieving carbon neutrality by 2050 | Three times a year |
Subcommittee for Promote the Reduction of CO2 from Business Activities | Draft action plans for reducing CO2 in areas of business activity, promotion of specific measures, etc. | Twice a year |
TCFD Consideration Team | Identify and assess climate-related risks and opportunities, consider scenario analysis, etc. | Meets as necessary |
Strategy
Risks and Opportunities
a. Short-, medium- and long-term climate-related risks and opportunities the organization has identified
The Group considers climate-related risks and opportunities to be an important perspective in the formulation of our business strategy. We are identifying and evaluating short-, medium-, and long-term risks and opportunities, as well as analyzing the impact on our business based on multiple climate scenarios. We are also considering countermeasures in response to these risks and opportunities.
As particularly high-impact migration risks, we identified the “strengthening of regulations for fuel economy/CO2 and zero-emission vehicles” and the “introduction and expansion of carbon pricing.” We identified “increasing frequency and intensity of meteorological disasters” as a physical risk. While these risks may affect our business in various ways, we recognize that responding appropriately to these risks will lead to greater sales of electrified vehicles*1 and new business opportunities.
- Electrified vehicles: Battery-powered electric vehicles, plug-in hybrid electric vehicles (PHEV), and hybrid electric vehicles (HEV)
Identified climate-related risks and opportunities
Type | Item | Assumed Impact on MITSUBISHI MOTOR’S Business Activities | Timing of the Impact*2 |
Degree of impact | |
---|---|---|---|---|---|
Transition risks | Policy and legal | Strengthening of regulations for fuel economy/CO2 and zero-emission vehicles |
|
Short/medium/long term | Large |
Introduction and expansion of carbon pricing |
|
Medium/long term | Large | ||
Technology | Investment in new technologies |
|
Short/medium/long term | Medium | |
Market | Changes in the energy mix |
|
Medium/long term | Small | |
Tight supply and demand for raw materials (rare metals) |
|
Medium/long term | Medium | ||
Changes in user awareness and behavior |
|
Medium/long term | Medium | ||
Reputation | Increasingly stringent assessment by ESG rating institutions and stakeholders |
|
Short/medium term | Medium | |
Physical risks | Acute | Increasing frequency and intensity of meteorological disasters |
|
Short/medium/long term | Large |
Chronic | Rise in average temperatures |
|
medium/long term | Small | |
Rise in ocean levels |
|
Medium/long term | Medium | ||
Opportunities | Products and services | Growing demand for electrified vehicles |
|
Medium/long term | Large |
Energy source | Advancement in energy technologies |
|
Short/medium/long term | Medium |
- Short term: Up to three years; medium term: three to 10 years; long-term: more than 10 years. Some issues impacts have already occurred as a result of the recent international situation.
- A general term encompassing vehicle to home (V2H) and vehicle to grid (V2G), among others
b. Impact of climate-related risks and opportunities on the organization’s business, strategy, and financial planning
With the vision of “creating vibrant society by realizing the potential of mobility,” the Group aims to enhance our corporate value over the long term by providing products with value that is unique to MITSUBISHI MOTORS through contributions to carbon neutrality and other efforts. As society-wide efforts to achieve carbon neutrality accelerate, we recognize that climate-related matters may affect our business, strategies, and financial plans, so we periodically review our strategies and plans as appropriate based on climate change risks and opportunities.
c. Resilience of the organization’s strategy, taking into consideration different climate-related scenarios, including a 2℃ or lower scenario
Based on climate scenarios and future information from organizations such as the International Energy Agency (IEA), the Intergovernmental Panel on Climate Change (IPCC), and the Network for Greening the Financial System (NGFS), MITSUBISHI MOTORS considered the “less than 2℃ scenario*4,” which assumes actions by society to avoid climate change as of 2030 and 2050. We also looked at a “growth scenario*5,” which assumes national policies continue to grow more stringent. Under these scenarios, we examined the risks and opportunities, focusing on areas with significant impact on our business activities.
The results of analysis related to the impact on our business of the associated risks and opportunities are as described on the following page.
- Referenced the IEA’s Announced Pledges Scenario (APS), the IPCC’s “RCP4.5,” the NGFS’ “Net Zero 2050,” etc.
- Referenced the IEA’s Stated Policies Scenario (STEPS), the IPCC’s “RCP8.5,” the NGFS’ “Current Policies,” etc.
Impact on strategies and plans
Business area | Recognized impact | Incorporation into strategies and plans |
---|---|---|
Products and services | To realize a carbon-neutral society, various countries and regions are strengthening regulations for fuel economy/CO2 and zero-emission vehicles. These will affect our product development, production and procurement strategies. | In 2020, we formulated the Environmental Targets 2030, which set the target of achieving a 40% reduction in CO2 emissions from new vehicles (compared with FY2010 levels) and a target ratio of electrified vehicle sales of 50% by FY2030. In February 2023, we set a new target, raising our target ratio of electrified vehicle sales to 100% by FY2035. Meanwhile, in our mid-term business plan, “Challenge 2025” we set a target of introducing nine electrified vehicle models by FY2028. |
Supply chain, value chain | In the automobile manufacturing and sales business, greenhouse gases such as CO2 are emitted not only during the manufacture of products, but throughout the entire value chain. As climate change advances, the worldwide risk of increasingly frequent and severe occurrences, such as typhoons and floods, is mounting. If our supply chain or value chain is affected by such events, our plants’ operations and sales could be affected. |
We revised our Environmental Targets 2030 in February 2023, adding the procurement target of “promoting CO2 reduction activities with major business partners,” and the logistics target of “promoting CO2 reduction activities in cooperation with transportation companies.” |
Investment in R&D | We are promoting investment in R&D to address increasingly stringent and new regulations for fuel economy/CO2 and zero-emission vehicles in the countries and regions where we operate. These moves will affect our R&D costs for electrified vehicles and other products. | In our mid-term business plan, “Challenge 2025,” we are budgeting ¥70.0 billion in R&D expenses related to electrification in FY2025. We have also earmarked ¥55.0 billion in capital expenditures related to electrification. |
Adaptation and mitigation measures | Our business could be affected by countries and regions introducing or expanding carbon taxes and emissions trading systems, as well as by rising energy costs. | In 2020, we formulated the Environmental Targets 2030 and set the goal of reducing CO2 emissions from our business activities “by 40% compared to FY2014.” In February 2023, we raised this figure to “a reduction of 50% compared to FY2018,” the SBT*6 target equivalent to a 1.5°C level. |
- SBT: Short for Science Based Targets, which are greenhouse gas emission reduction targets set by companies consistent with the Paris Agreement levels
Impact of Risks and Opportunities on the MITSUBISHI MOTORS Group’s Business Activities
Scenario | Item | Risks/Opportunities | Impact on MITSUBISHI MOTORS’ business | Key countermeasures | |
---|---|---|---|---|---|
Less than 2°C | Strengthening of regulations for fuel economy/CO2 and zero-emission vehicles | Risks |
|
|
|
Opportunities |
|
|
|
||
Introduction and expansion of carbon pricing | Risks |
|
|
|
|
Opportunities |
|
|
|||
Growth | Increasing frequency and intensity of meteorological disasters (flooding, inundation) | Risks |
|
|
|
Opportunities |
|
|
|
The MITSUBISHI MOTORS Group’s Response Measures Based on Risks and Opportunities
The Group will incorporate measures to address climate related risks and opportunities into our Environmental Plan Package and business strategies, which set forth the direction and goals of our environmental initiatives. In this way, we are promoting initiatives to reduce future risks, ensure sustainable business growth and enhance our resilience as a company.
On the product front, we will take our own plug-in hybrid electric vehicles (PHEV) and commercial electric vehicles in the Kei-car segment as a starting point, and leveraging the Allian’s technologies. We will develop electrified vehicles and promote fuel-efficient internal combustion vehicles, proactively introducing electrified vehicles that optimally meet customers’ needs, taking into consideration the energy situation and infrastructure development status in each country and region. Working toward carbon neutrality is one of the key challenges stated in “Challenge 2025,” our mid-term business plan. We will develop electrified vehicles and step up our efforts in the Alliance as we work toward the second phase of our plan to reinforce electrified vehicles (FY2026–FY2028). By FY2028, we plan to introduce nine electrified vehicle models. To date, we have introduced five: the “ASX PHEV/HEV models,” the “COLT HEV model,” the “XPANDER HEV model,” the “XPANDER CROSS HEV model,” and the “XFORCE HEV model.” Including models launched prior to February 2023̶ the “MINICAB EV/L100 EV,” “eK X EV,” “OUTLANDER PHEV model,” and “ECLIPSE CROSS PHEV model” -we offer a total of nine electrified vehicle models as of March 2025. In light of the global slowdown in the growth of battery EVs since 2024, we have adopted a policy of utilizing mainly OEM-supplied models from partners for battery EVs for the time being, and will concentrate our development efforts on PHEVs and HEVs, where we have a competitive advantage.
In our business activities, we are promoting energy minimization and the transition to renewable energy sources, and are working to reduce CO2 emissions.
Across the supply chain, we will collaborate with business partners, related companies and organizations, and governments and municipalities to reduce CO2 emissions at the production stage (through raw materials and parts) and in logistics (including products). We are also promoting renewable energy and charging infrastructure, utilize carbon-neutral fuel and promote V2X*7.
We believe the spread of electrified vehicles represents a chance to do new business in the form of reuse of used batteries, energy management, and data business using vehicle driving and battery data, and in collaboration with our partners and municipalities we will grow a mobility business that contributes toward the realization of a carbon-neutral society, which represents a unique opportunity for us as an automotive maker, into a fourth pillar of revenue after vehicle sales, financing (leasing), and after sales.
- V2X: A general term encompassing vehicle to home (V2H) and vehicle to grid (V2G), among others
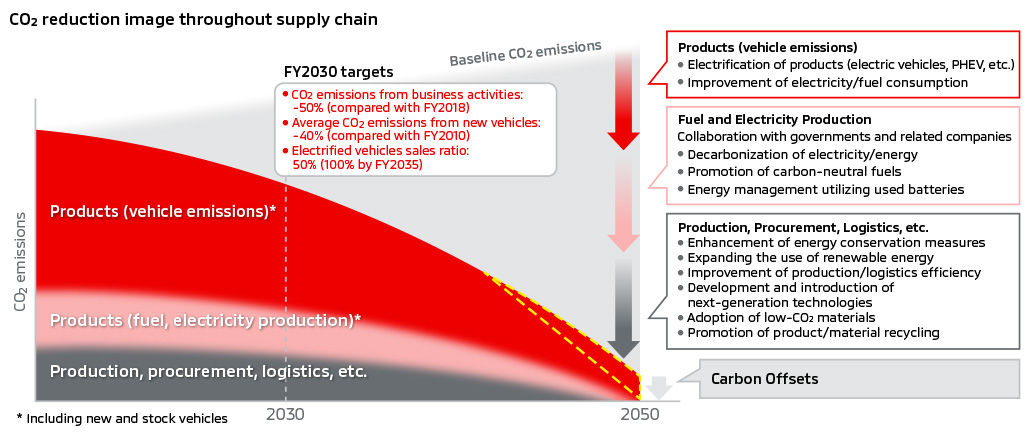
Risk Management
a. Organization’s processes for identifying and assessing climate-related risks
The Group has established a cross-functional team under the Sustainability Committee to conduct scenario analysis based on the recommendations of the Task Force on Climaterelated Financial Disclosures (TCFD). We have identified and assessed climate-related risks and opportunities that could affect our business, considering their potential occurrence and impact levels. We have incorporated goals and action plans for addressing climate-related risks and opportunities that have a particularly significant impact, and are monitoring progress through the Sustainability Committee.
b. Organization’s processes for managing climate-related risks
The climate-related risks, opportunities, and corresponding measures identified by the Sustainability Committee have been assigned to responsible executives at the executive officer level. We have set KPI and are implementing a PDCA cycle. Additionally, reports on critical risks and opportunities requiring prompt action are provided to the Board of Directors, which decides on appropriate responses.
In FY2018, we identified material issues that we should address, involving various problems related to fields of the environment, society, and governance. We have positioned “responding to climate change and energy issues” as one of the most critical material issues, and we are stepping up our efforts in this regard across the Group.
c. How process of identifying, assessing, and managing climate-related risks are integrated into the organization’s overall risk management
Risks affecting our business are managed throughout the Group and include risks related to the effects of climate change. In addition, the Internal Control Committee manages operational hazard risk, based on the annual “Companywide Risk Survey.”
Metrics and Targets
a. Metrics used by the organization to assess
climate-related risks and opportunities in line with its strategy and risk management process
The MITSUBISHI MOTORS Group formulated the Environmental Plan Package in 2020. Through electrified vehicles and the increased use of renewable energy, we aim to become carbon neutral by 2050 and contribute to the realization of a society that is resilient to climate change. We also formulated the “Environmental Targets 2030,” which clarifies specific initiatives to be achieved by 2030 in accordance with this vision. As major indices to be monitored and evaluated under “Action to Climate Change, we have established "CO2 emissions from business activities" for Scope 1 and 2*8, and "average CO2 emissions from new vehicles" and "ratio of electrified vehicle sales" for Scope 3*8 Category 11 (use of sold products) as key indicators for management and evaluation purposes.
In an effort to reinforce sustainable management, aimed at ensuring the Group’s sustainable growth, in FY2022 we added ESG-related items to an index used to determine the mediumto long-term performance-linked compensation for executive officers. In relation to the environment, we introduced “CO2 emissions from business activities” as an indicator to measure progress in addressing the escalating climate.
To move forward on efforts to reduce CO2 emissions, we introduced ICP (Internal Carbon Pricing:¥18,000 per ton of CO2) for domestic sites from FY2024, taking into account IEA and other international carbon prices. We use this as one of the factors for consideration when making decisions on capital investment.
- Scope 1 : A company’s direct emissions (such as from burning fuel)
Scope 2: Indirect emissions, resulting from electricity, heat or steam provided by another company
Scope 3: Scope 3: Indirect emissions other than Scope 1 and Scope 2 (Such as emissions due to the use of sold products)
b. Scope 1, 2 and 3 GHG emissions and related risks
MITSUBISHI MOTORS Group calculates CO2 emissions based on a GHG protocol. The table below shows the actual CO2 emissions for Scope 1, 2, and 3 in FY2018 (the base year for our CO2 emissions reduction target from business activities) and from FY2021 to FY2024.
To ensure our information is reliable and transparent, we have obtained independent third-party assurance for our Scope 1 and 2 emissions, as well as for Scope 3, Category 11 (use of sold products).
Scope 1, 2 and 3 Emission
Unit | FY2018 | FY2021 | FY2022 | FY2023 | FY2024 | |
---|---|---|---|---|---|---|
Scope1 | x103 t-CO2 | 119 | 92 | 95 | 90 | 85 |
Scope2 | x103 t-CO2 | 469 | 319 | 271 | 264 | 243 |
Scope3 | x103 t-CO2 eq | 42,580 | 28,294 | 28,710 | 31,743 | 29,713 |
Total | x103 t-CO2 eq | 43,168 | 28,705 | 29,076 | 32,097 | 30,041 |
c. Targets used by the organization to manage climate-related risks and opportunities and performance against targets
Major FY2030 Targets and Progress
Indicators | FY2030 Target |
FY2035 Target |
FY2023 Result |
---|---|---|---|
Average CO2 emissions from new vehicles (Tank to Wheel) |
–40% (Compared to FY2010) |
- | –19% (Compared to FY2010) |
Ratio of electrified vehicles sales | 50% | 100% | 16% |
CO2 emissions from business activities (Total Scope1 and 2) |
–50%*9 (Compared to FY2018) |
- | -40% (Compared to FY2018) |
- FY2018 Scope 1 and Scope 2 emissions of 588 thousand t-CO2 include emissions of 43 thousand t-CO2 from certain equity-method associates.
In March 2023, we reviewed our targets in line with the latest perspectives on selecting companies subject to environmental management. After subtracting emissions from these equity-method associates, we revised our base figure to 545 thousand t-CO2.
Development and Spread of Electrified Vehicles
In our Environmental Targets 2030, the Group set the target of achieving a 40% reduction in average CO2 emissions from new vehicles by 2030 (compared with FY2010 levels). To meet this target, we are positioning electrified vehicles, which emit low CO2 while driving, as a core technology in responding to climate change and energy issues, and are advancing their development while also aiming to raise the electrified vehicle sales ratio to 50% by FY2030 and to 100% by FY2035. Centering on our strength in plug-in hybrid electric vehicles (PHEV), we will expand our lineup of electrified vehicles, thereby promoting their popularization and use in society and contributing toward the realization of a sustainable society.
Electric Vehicles (EV)
Electric vehicles (EV) are driven by electricity in battery, so they emit no exhaust gases such as CO2 while driving.
We released the “i-MiEV” as the world’s first mass-produced EV in 2009. In addition to its environmental performance, the “i-MiEV” performed better than conventional gasoline engine vehicles on quietness and acceleration starting from maximum torque. In 2011, we launched the “MINICABMiEV,” a Kei-car segment commercial electric EV. In 2012, we began offering the “MINICABMiEV TRUCK,” also an EV in the Kei-car segment. These technologies are the foundation of next-generation EVs, such as PHEV.
We believe that expanding the lineup of Kei-car EVs, which are expected to be used in more everyday situations, will be the key to the spread of electrified vehicles. Accordingly, in June 2022 we launched the “eK X EV,” a new EV in the Kei-car segment, and in December 2023 we launched the “MINICAB EV,” new commercial EV in the Kei-car segment.
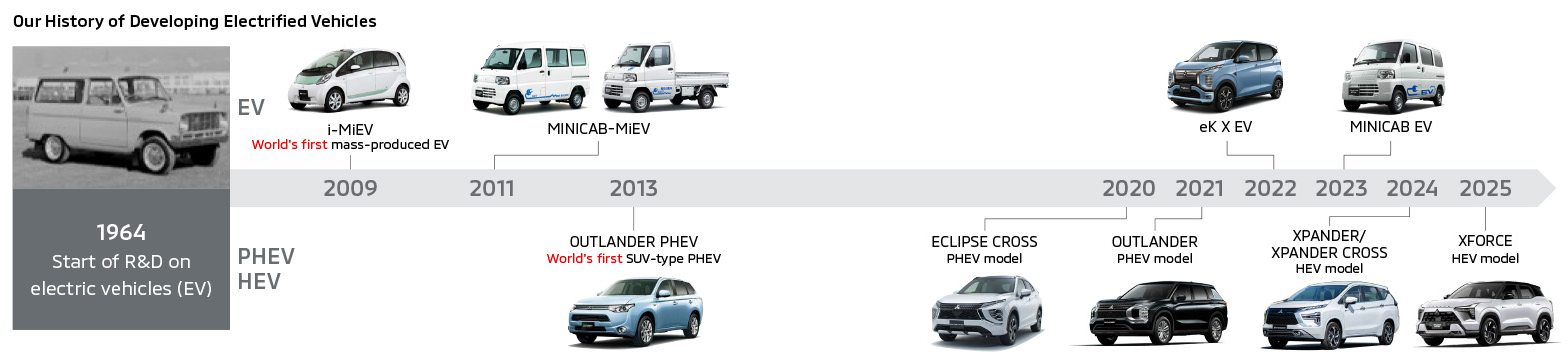
Plug-in Hybrid Electric Vehicles (PHEV)
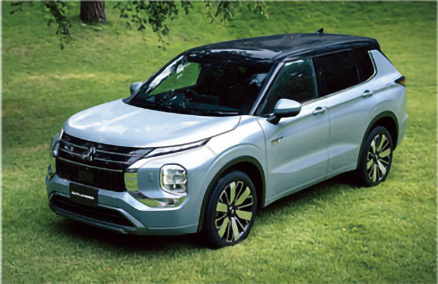
OUTLANDER PHEV
Electric vehicles (EV) are driven by electricity in battery, so they emit no exhaust gases such as CO2 while driving.
We released the “i-MiEV” as the world’s first mass-produced EV in 2009. In addition to its environmental performance, the “i-MiEV” performed better than conventional gasoline engine vehicles on quietness and acceleration starting from maximum torque. In 2011, we launched the “MINICABMiEV,” a Kei-car segment commercial electric EV. In 2012, we began offering the “MINICABMiEV TRUCK,” also an EV in the Kei-car segment. These technologies are the foundation of next-generation EVs, such as PHEV.
We believe that expanding the lineup of Kei-car EVs, which are expected to be used in more everyday situations, will be the key to the spread of electrified vehicles. Accordingly, in June 2022 we launched the “eK X EV,” a new EV in the Kei-car segment, and in December 2023 we launched the “MINICAB EV,” new commercial EV in the Kei-car segment.
Hybrid Electric Vehicles (HEV)
MITSUBISHI MOTORS’ HEV system offers EV mode, series hybrid mode, parallel hybrid mode, and regenerative mode. The system automatically selects the optimal driving mode according to driving conditions and remaining drive battery capacity to achieve low fuel consumption and powerful and pleasant motor drive.
When starting off or at low speeds, in EV mode the vehicle runs on electric power alone, with the drive battery supplying power to the motor. In series hybrid mode, when the vehicle is climbing or accelerating, the engine is used to generate electricity, and the motor is used to drive the vehicle in combination with power from the drive battery. At higher speeds, the system switches to parallel hybrid mode, in which the car runs on engine power and is assisted by the motor. In regenerative mode, the vehicle recovers energy from deceleration, which it converts into electric power and stores in the drive battery.
In FY2024, we began launch of the new "ASX HEV model" in Europe and the new "XFORCE HEV model" in Thailand.
Promoting the Use of Electrified Vehicles as a Way of Adapting to Climate Change
By leveraging the large-capacity batteries on its electric vehicles (EV) and PHEV and their power supply functions, we are promoting adaptation measures to climate change and energy issues in collaboration with other industries. We are applying these to such areas as energy management, V2X*10 and use as emergency power sources in times of disaster.
- V2X: A general term encompassing vehicle to home (V2H) and vehicle to grid (V2G), among others
TOPICS
Demonstration Testing of Two Concepts for Energy Storage Utilization in Conjunction with Chargers for Electrified Vehicles
In January 2023, we installed demonstration facilities for two concepts linked to quick chargers and bi-directional chargers for electrified vehicles in the M-Tech Lab*11, a smart grid demonstration facility at the Okazaki Plant, where we are conducting demonstration tests.
Both systems utilize used battery modules. One is an energy storage system that connects to the power line of a quick charger and discharges stored power to reduce power peaks when fast-charging electrified vehicles. The other is an energy storage unit, which is connected to a bidirectional charger in a CHAdeMO*12 standard. This unit stores energy even when the electrified vehicles are away, facilitating efficient energy management. Through demonstration testing, we will establish technical requirements for safely and more effectively utilizing used batteries under various conditions. In the future, we will work with energy storage equipment manufacturers to introduce these systems at Group dealers' shops and other locations.
-
Demonstration facility for utilizing used batteries
-
M-Tech Lab
- M-Tech Lab: Test equipment for a smart grid demonstration, our first initiative utilizing used batteries, began operating in April 2012.
- CHAdeMO: A quick-charging system for electric vehicles, a global standard that Japan led the way in standardizing in 2010.
TOPICS
Launch of a Commercial Smart Charging Service Employing Our Connected Technologies for Electrified Vehicles
MITSUBISHI MOTORS, MC Retail Energy Co., Ltd., Kaluza Japan, and Mitsubishi Corporation launched Japan’s first*13 commercial smart charging service using connected technologies from our electrified vehicles in October 2024.
- As of July 2025, according to our research, this refers to the use of connected vehicle technologies in a controlled charging service.
Features of the Service
This service optimizes the charging of OUTLANDER PHEVs in line with electricity prices by connecting MITSUBISHI MOTORS’ connected systems to an advanced energy software platform provided by Kaluza Japan. The service is available through subscriptions to MC Retail Energy’s EV smart-charging plans for households.
■Benefits to Customers
-
Daily smart charging
Simply by connecting OUTLANDER PHEVs to a home charging station and setting intended departure time via the smartphone app, customers can enable the system to automatically control the charging schedule.
-
Points system based on use of controlled charging
Some of the cost savings achieved through optimized charging with this service will be returned to customers in the form of electricity-bill discounts.
■Benefits to Society
-
Effective use of renewable energy
By charging during periods of low electricity prices, the system helps make use of surplus renewable energy and indirectly contributes to the more effective renewables.
-
Efficient “peak-hour” shifts
By controlling charging, this service helps to shift the hours of peak electricity loads and contributes to the efficient operation of power grid infrastructure.
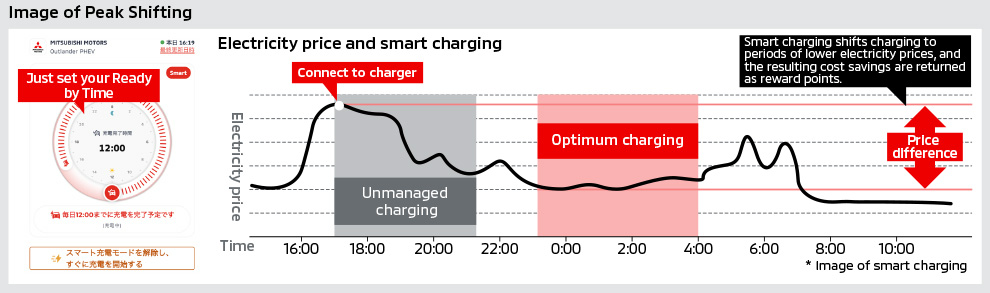
TOPICS
Launch of Joint Demonstration of Movable Storage Batteries Utilizing Used Batteries
In September 2023, MITSUBISHI MOTORS and Hitachi, Ltd. began joint demonstration testing of the “Battery Cube”,*14 a movable storage battery that utilizes used batteries from electrified vehicles. In this demonstration, used batteries from OUTLANDER PHEVs are installed in the Battery Cube. In preparation for power outages during large-scale disasters, power from the Battery Cube is used to operate the “Urban Ace HF”, Hitachi’s standard elevator. In addition to supplying power from electrified vehicles equipped with V2H functionality, this combination using a Battery Cube should help to ensure continuous backup power supply in case of disaster.
We aim to commercialize Battery Cube with Hitachi in FY2025. We will work together to introduce Battery Cube to companies and local governments. We are also planning a joint demonstration for energy management that connects electrified vehicles and Battery Cube with solar panels and other devices to make effective use of renewable energy.
- Battery Cube: Registered trademark of Hitachi High-Tech Corporation in Japan
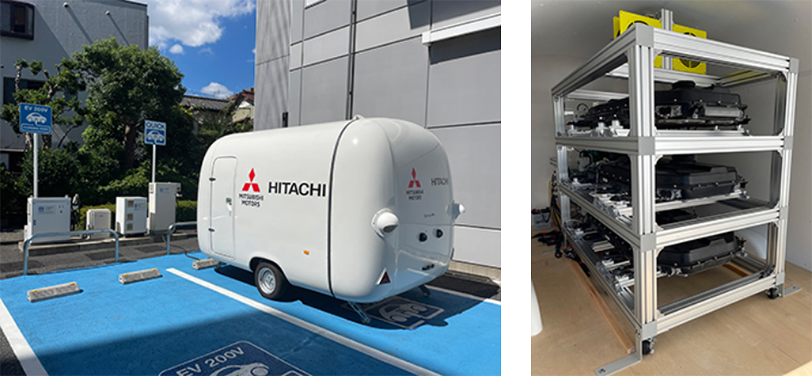
Left: Battery Cube supplying electricity
Right: Used batteries inside the Battery Cube
TOPICS
Launch of Self-Directed Light That Utilizes Used Batteries from Plug-in Hybrid Vehicles (PHEV)
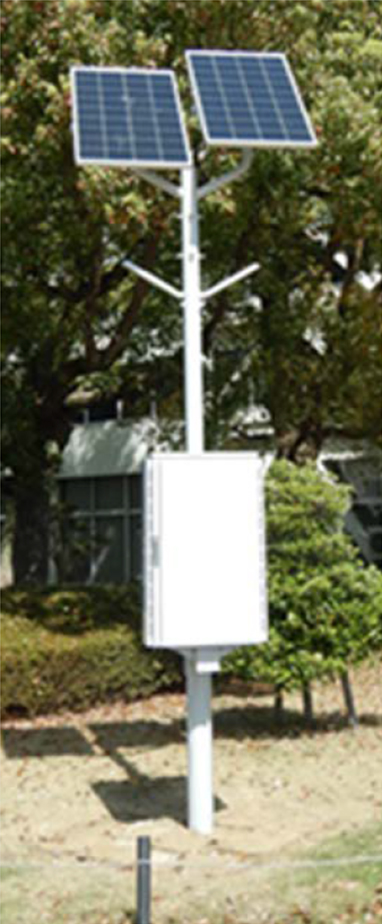
Self-directed light
MITSUBISHI MOTORS and MIRAILABO Co., Ltd. have been developing a self-directed light using used PHEV batteriesaiming to contribute to decarbonization by promoting the use of renewable energy. Our self-directed lights store solar power generated during the day in used PHEV batteries, using the power to illuminate LED lights at night. Since they do not require an external power supply, they continue to operate independently in the event of a disaster or power failure. Used batteries mean that CO2 emissions from battery production are lower than for streetlights using new batteries, and CO2 emissions during operation are zero, as the electricity comes from solar power.
In FY2022 and FY2023, MITSUBISHI MOTORS conducted a demonstration project that involved installing 24 self-directed lights at the facilities of the Okazaki Plant, Mizushima Plant, Kyoto Plant, and Tokachi Research & Development Center. In March 2025, based on the results of the demonstration, we sold the first self-directed light to Okazaki City in Aichi Prefecture. As part of its Decarbonization Leading initiative, the city installed the light at the Social Welfare Council Service Center.
Development of Improving Fuel Economy Technologies
MITSUBISHI MOTORS is continuously promoting the development of powertrain technologies to reduce fuel consumption and improve energy efficiency.
Idle Reduction System “AS&G” (Auto Stop & Go)
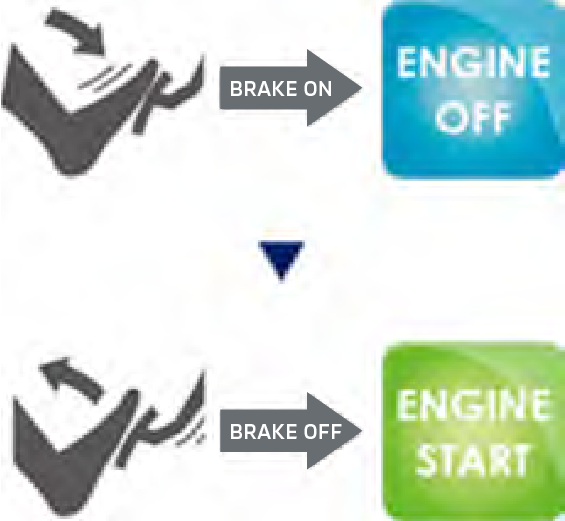
AS&G is an idle reduction system that automatically stops and starts the engine. This has a major effect on improving the fuel economy because no fuel is consumed when at a stop. When fitted with a coasting stop function, AS&G stops the engine while decelerating.
Deceleration Energy Recovery (Power Generation Control)
This technology involves the intensive charging of the battery using electric power generated while decelerating. This reduces the amount of power required from the engine, thereby improving fuel economy.
Hybrid System
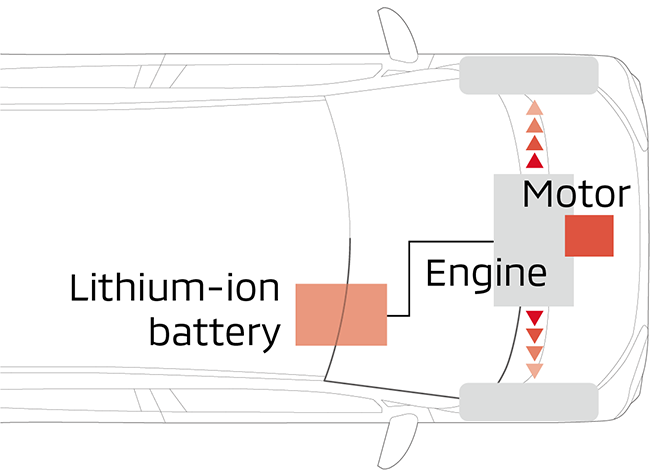
Hybrid system on the “eK X”
The eK series (excluding the “eK WAGON”) uses MITSUBISHI MOTORS’ 12V BSG*15 hybrid system. The power produced by regenerative energy during deceleration is used to efficiently charge the lithium-ion battery, and the motor assists the engine during acceleration to achieve torquey and fuel-efficient driving and smooth engine stopping and starting.
The new “OUTLANDER” uses 48V BSG hybrid system specifications, generating more power from the energy of deceleration.
- Short for “belt-driven starter generator,” the BSG adds motor functionality to the generator, using a belt drive to assist engine startup and providing power assistance.
Variable Valve Timing Mechanism Mitsubishi Innovative Value timing Electronic Control System (MIVEC)
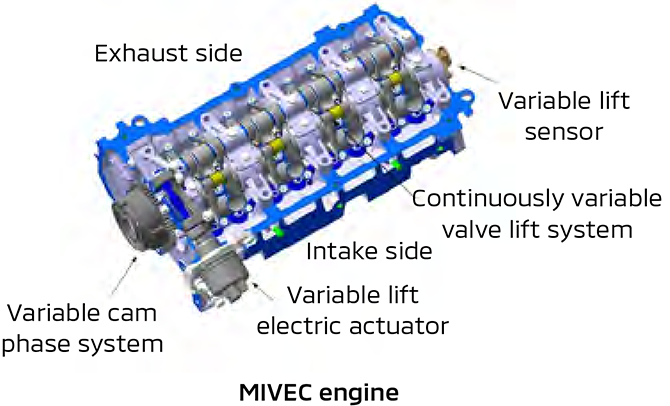
MIVEC engine
The MIVEC is a variable valve timing mechanism for minimizing fuel consumption. The intake valve lift is continuously varied according to the operating condition to minimize air intake energy loss, resulting in improved fuel efficiency.
Gasoline Direct-Injection Turbo Engine
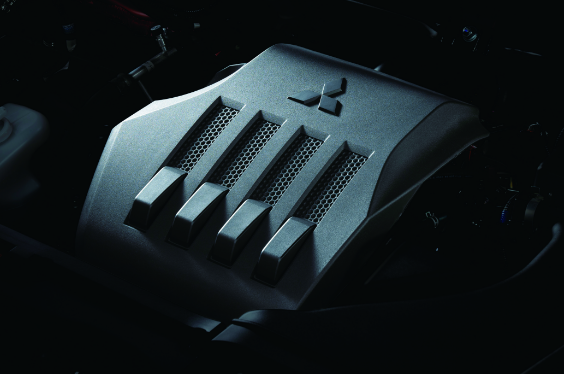
Direct injection turbocharged gasoline engine (4B40)
The “ECLIPSE CROSS” adopts a 1.5L downsized direct-injection turbo engine (4B40). By precisely controlling in-cylinder injection and intake port injection based on driving circumstances, this engine delivers superior fuel economy and a clean exhaust gas. By combining an exhaust manifold integrated with the cylinder head, intake and exhaust MIVEC, and a compact turbocharger with an electric wastegate actuator, the engine optimizes supercharging pressure control to respond as the driver demands, thus delivering a comfortable and powerful driving.
The new “OUTLANDER” is also equipped with a next-generation 1.5L downsized direct injection turbocharged gasoline engine, which is an improved version of the 4B40 engine. Additionally, it is combined with a hybrid system that incorporates a 48V BSG. This system assists the engine during start-up and acceleration with the motor, achieving a high level of performance and fuel efficiency.
Clean Diesel Turbo Engines
The new “TRITON” we launched in Thailand in July 2023 is equipped with a new 2.4L diesel turbo engine. The weight and friction losses of the engine are reduced due to the optimally designed key components such as the cylinder block, piston and connecting rods. Additionally, the fuel injection system has been upgraded to the next generation, providing high performance while achieving excellent fuel efficiency and clean exhaust gas characteristics.
In February 2024, we added a higher-output version of the engine with a two-stage turbocharger. With a maximum output of 150 kW and maximum torque of 470 Nm, it delivers powerful acceleration and abundant torque that rises responsively from low to mid-range speeds.
New Gasoline Engine for Electrified Vehicles
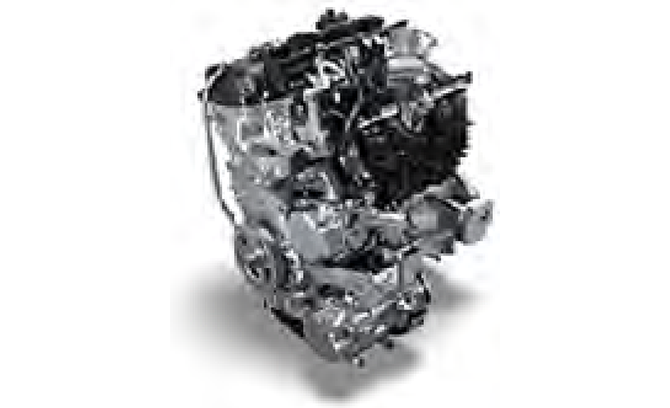
1.6L gasoline engine for electrified vehicles
The HEV models of “XPANDER” and “XPANDER CROSS” that went on sale in Thailand in February 2024 are powered by a newly developed 1.6L gasoline engine for electrified vehicles. A high expansion ratio cycle (Atkinson cycle*16) is used to improve combustion efficiency, and an electric water pump has been adopted for the first time in a MITSUBISHI MOTORS engine to eliminate the auxiliary drive belt and reduce mechanical losses.
- Atkinson cycle: A type of internal combustion engine that uses a higher expansion ratio than compression ratio to reduce exhaust heat and improve thermal efficiency.
Taking the Initiative in Business Activities Toward Carbon Neutrality
To achieve carbon neutral, the Group will approach the issue from both the “demand side” (energy consumption) and the “supply side” (energy generation and procurement). To ensure our activities are carried out systematically, we have formulated a medium- to long-term roadmap toward carbon neutrality. Following this plan, we are working to develop future technologies, improve production processes and expand the introduction of renewable energy.
We have established the Subcommittee to Promote the Reduction of CO2 as an infrastructure of the Sustainability Committee. The subcommittee, which has members from production, development and dealers in Japan and overseas, aims to help the entire MITSUBISHI MOTORS Group achieve carbon neutrality in its business activities. Beside sharing information on the progress of action plans, actual CO2 emissions, and other pertinent data. The committee also drafts reduction measures, considers future technologies, and deliberates the future energy mix.
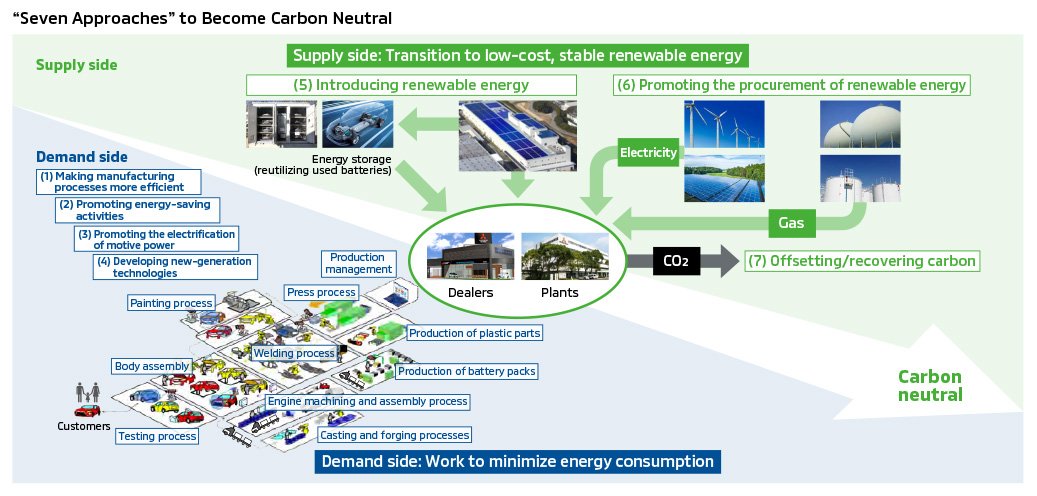
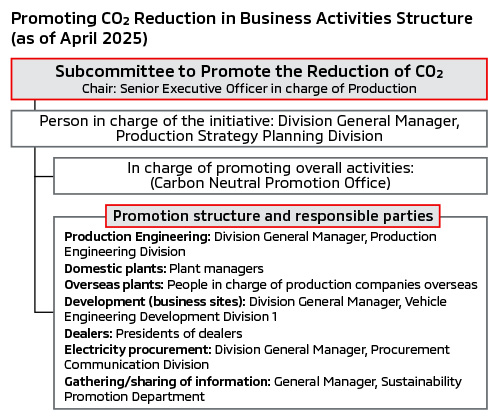
Introduction of Renewable Energy
The MITSUBISHI MOTORS Group is actively seeking to use renewable energy in its operations, taking into consideration the energy situation at each site. To do so, we are introducing in-house renewable energy generation and purchasing renewable energy from energy suppliers.
We believe solar power offers us an important way to achieve carbon neutrality, and we are proactively introducing solar power generation at our locations. In addition, we began introducing electricity derived from renewable energy sources for some of our domestic and overseas production facilities, and we plan to gradually expand this initiative going forward.
TOPICS
Starting to Use Solar Power Generation Equipment (Rooftop of the Plant)
In FY2024, a new 0.5 MW solar panel system was installed at the Kyoto Plant in Japan, increasing the Group’s total renewable energy generation capacity to approximately 33 MW. The Group’s total electricity generation from renewable sources reached 36,823 MWh during the year, accounting for 6% of its overall electricity consumption.
Additionally, we have begun trial installation of significantly lighter solar panels at our domestic manufacturing sites. These lightweight panels reduce the load on buildings, and we plan to explore further expansion of renewable energy adoption based on the results of these trials.
Initiatives at Manufacturing Plants
To reduce CO2 emissions from production activities, we have established a medium- to long-term roadmap to achieve carbon neutrality in each area of production technology̶pressing, welding, painting, assembly and powertrain̶and we are developing future technologies and improving production processes to this end. We are incorporating measures such as production efficiency improvements and the introduction of energy-saving equipment into our capital investment plans and implementing them to promote energy conservation in the production process. In energy-saving activities involving participants from production sites, production technology, and power supply department, we are working on operational improvements and loss prevention following the introduction of new equipment.
TOPICS
Optimizing Operational Control of the Painting Process (Okazaki Plant)
At the Okazaki Plant, MITSUBISHI MOTORS has substantially revised how we manage the painting process, and we are undertaking thorough initiatives toward energy conservation.
Quality control during the painting process requires that air control be closely monitored. We have carefully reviewed individual conditions and introduced revisions to temperature and humidity, reducing air speed and intermittent operation, employing blowers in processes that use compressed air, and controlling air conditioning in response to the temperature and humidity of the outside air.
As a result of these efforts, we expect to reduce energy consumption throughout the overall painting process by approximately 10% and reduce CO2 emissions by 3,500 tons per year. Going forward, we will apply the knowledge we gain at the Okazaki Plant to other sites.
-
Bird’s-eye view of the paint plant at the Okazaki Plant
-
Overview of the Painting Process and Energy Inputs
Efforts to Reduce Air Consumption (Kyoto Plant)
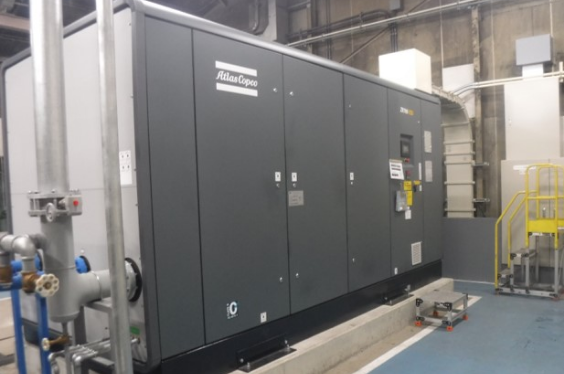
Upgraded inverter-type compressor
The compressors used to produce compressed air account for about 20% of the energy used by the Kyoto Plant. Accordingly, decreasing the plant’s consumption of compressed air is a priority for reducing CO2 emissions.
In FY2023, we focused on reducing the amount of compressed air wasted in the casting process. We introduce such measures as the intermittent use of air for cooling and cleaning. We also expanded the rotary water drainage system, which we found to be highly effective in FY2022, to other lines, and installed three new units. Furthermore, we upgraded our compressor, improving the energy efficiency of the compressed air supply.
These measures are expected to reduce compressor power consumption by more than 15% and CO2 emissions by approximately 2,800 tons per year.
Office Initiatives
We are also promoting the use of renewable energy and introducing various types of energy-saving equipment in areas other than manufacturing, such as at R&D and head office locations. Part of the electric power used at the Research and Development Building (Okazaki, Aichi Prefecture) and head office (Minato-ku, Tokyo) is supplied by renewable energy, thanks to the erection of rooftop solar power system and making use of the Tradable Green Certificates System*17. Also, CO2 emissions are being reduced by using energy-saving electrical equipment and air conditioners. In 2020, we began tracking electricity use and power generation per capita at our Research and Development Building, comparing these figures with other offices, and using digital signage to show year-on-year comparisons by month. In these ways, we are working to increase employee awareness about saving energy
- This system is used to trade environmental added value of renewable energy generated from natural energy sources using renewable energy certificates issued by a certificate issuer and confirmed by a third-party organization
Digital signage at Research and Development Building (Okazaki)
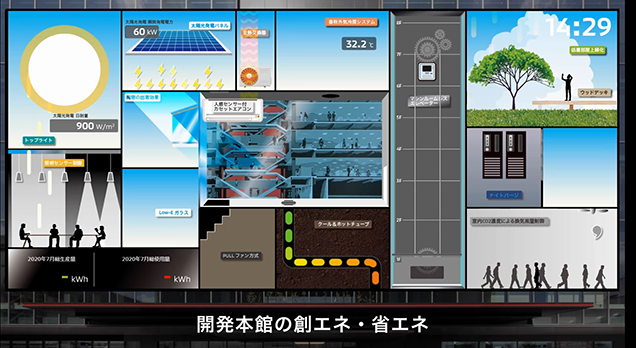
Dealer Initiatives
We encourage our dealers in Japan to acquire Eco-Action 21*18 certification and carry out activities such as reducing the amount of energy and water they use, lowering the amount of waste they produce, and promoting the widespread use of electrified vehicles.
We are expanding the nationwide rollout of DENDO DRIVE STATIONs̶next-generation dealerships where visitors can experience the appeal of electrified vehicles, including their use as power sources in times of disaster and their contribution to the environment.
- Eco-Action 21 is a certification and registration system based on the Environmental Management Systems guidelines formulated by the Japanese Ministry of the Environment
Dealers That Have Acquired “Eco-Action 21” Certification (As of the end of March, 2025)
Company | ||
---|---|---|
Aomori Mitsubishi Motor Sales Co., Ltd. | Shiga Mitsubishi Motor Sales Co., Ltd.*19 | Kyushu Mitsubishi Motor Sales Co., Ltd. |
Higashi Nihon Mitsubishi Motor Sales Co., Ltd. | Toyama Mitsubishi Motor Sales Co., Ltd. | Oita Mitsubishi Motor Sales Co., Ltd. |
Ibaraki Mitsubishi Motor Sales Co., Ltd. | Toyama Diamond Motors Co., Ltd. | Sobu Mitsubishi Motor Sales Co., Ltd. |
Kyoto Mitsubishi Motor Sales Co., Ltd. | Ishikawa Chuo Mitsubishi Motor Sales Co., Ltd. | Tokai Mitsubishi Motor Sales Co., Ltd. |
Nishi Nihon Mitsubishi Motor Sales Co., Ltd. | Gunma Mitsubishi Motor Sales Co., Ltd. | Sunen Mitsubishi Motor Sales Co., Ltd. |
- Certification received for the Kyoto Mitsubishi Motor Sales Co., Ltd. Group
TOPICS
Rolling out the DENDO DRIVE STATION across Japan’s Prefectures
We seek to put DENDO DRIVE STATIONs into operation in prefectures across Japan. DENDO DRIVE STATIONs are next-generation dealerships where visitors can experience the appeal of electrified vehicles, including their use as power sources in times of disaster and their contribution to the environment. In FY2024, we opened nine stations, bringing the nationwide total to 106. By deploying DENDO DRIVE STATION branches across Japan, we will increase the significance of electrified vehicles by diversifying their energy sources and communicating their value as sources of electric power in times of disaster.
-
Exterior
(Takamatsu Higashi Branch, Kagawa Mitsubishi Motors Sales Co., Ltd.)
-
Electrified Vehicle Charging Facilities
Electricity generated by the solar power system is used to charge electrified vehicles through V2H*20 equipment.
(Takamatsu Higashi Branch , Kagawa Mitsubishi Motors Sales Co., Ltd.) -
Lifestyle Corner
In a corner designed to look like a typical household dining area, we conduct a “1500W experience demonstration” to show how daily life can go one, even during disasters, by using just a 100V AC power supply (1500W) from an electrified vehicle.
(Shin Nanbu Branch, Kumamoto Mitsubishi Motor Sales Co., Ltd.)
- V2H: Vehicle to home, V2H is a system that enables electricity stored in a car’s battery to be supplied to the home
Physical Distribution
Capture and visualize Global Logistics CO2 Emissions
The Group is promoting initiatives to capture and visualize global logistics CO2 emissions across the supply chain, including overseas operations. In addition to the ongoing efforts to understand logistics CO2 emissions from overseas production plants, from FY2023, we expanded the scope to include overseas vehicle sales subsidiaries. Furthermore, we are analyzing the visualized logistics CO2 emissions and promoting initiatives to reduce emissions.
Working to Reduce CO2 Emissions from Logistics
The Group is promoting initiatives to reduce Logistics CO2 emissions in the transportation of production parts, after sales parts, and finished vehicles. Key logistics efficiency measures include not only improvements driven by our own efforts, such as packaging improvements and increasing transport loading rates, but also active and comprehensive initiatives through collaboration with logistics partners. These include promoting eco-driving, increasing the size of transport equipment, modal shifts, reducing transport distances through joint transportation with alliance partners, and shared use of logistics facilities. We have been implementing these initiatives proactively for some time. In addition to these proactive and comprehensive measures, we are considering collaborating more closely with logistics partners to encourage the introduction of vehicles that run on non-fossil fuels.
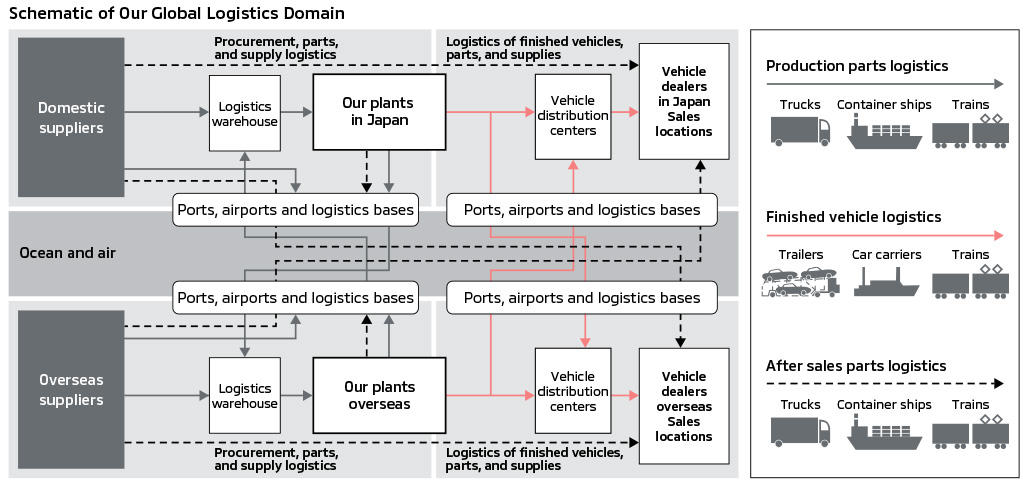
TOPICS
Initiatives to Reduce CO2 Emissions in Parts and Finished Vehicle Transportation
Improvement Example 1: Enlarge transportation equipment: Introduced full trailers
(Nakatsu, Oita Prefecture → Distribution center near MITSUBISHI MOTORS Mizushima Plant)

Distribution route: Nakatsu, Oita Prefecture → Distribution center near Mizushima Plant (Kurashiki, Okayama Prefecture), approx. 400 km
Previously: Large trucks |
After improvement: Full trailers |
Improvement effect | |
---|---|---|---|
Trips per month | 40 | 22 | Down by 18 |
Annual CO2 Emissions | 228t-CO2 | 150t-CO2 | Down by 78t-CO2 |
Improvement Example 2: Modal Shift That Utilizes Domestic Vessels*23
(Shin Moji Port → Osaka South Port)

Target logistics route: Kitakyushu area → Okazaki Plant (Okazaki, Aichi Prefecture), approx. 750 km
Previously: Transported by large trucks |
After improvement: Transported by domestic vessels |
Improvement effect | |
---|---|---|---|
Annual CO2 Emissions | 265t-CO2 | 111t-CO2 | Down by 154t-CO2 |
- Domestic vessel: Ship used for transport cargo within in Japan
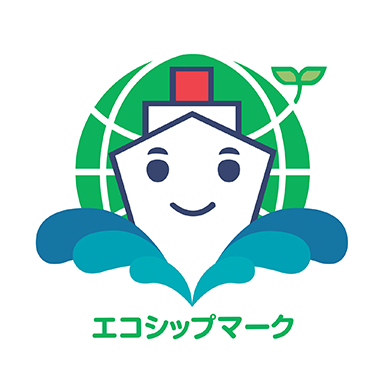
In addition, our use of domestic vessels for modal shift (Shin Moji Port to Osaka South Port) was commended by the Director-General of the Maritime Bureau of the Ministry of Land, Infrastructure, Transport and Tourism as an excellent operator in the “FY2023 Eco-Ship Modal Shift Project” organized by the Japan Long-Course Ferry Association, and was awarded the “Eco-Ship Mark” certification.
Improvement Example 3: Modal Shift: Use of Rail Freight Transportation
(Mizushima Plant → Niigata Prefecture)
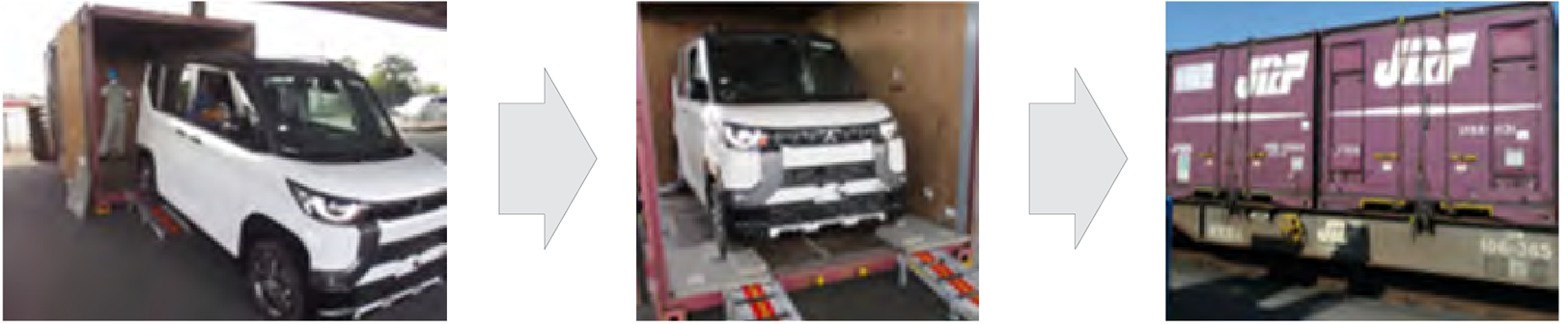
Target logistics route: Kurashiki Cargo Terminal Station → Niigata Cargo Terminal Station, approx. 790km
Previously: Transported by trailer |
After improvement: Transported by rail |
Improvement effect | |
---|---|---|---|
Annual CO2 Emissions | 10.8t-CO2 | 2.4t-CO2 | Down by 8.4t-CO2 |
Initiatives throughout the Supply Chain
The Group aims to become carbon neutral across the supply chain by 2050. To do so, it is essential that our suppliers reduce CO2 emissions.
In November 2023, we held a briefing session for our suppliers to share the Group’s initiatives toward carbon neutrality and deepened communication with suppliers handling items with high CO2 emissions and emissions reduction. By the end of FY2024, we had supported concrete activities to reduce CO2 emissions at three supplier companies. We also invited suppliers to our in-house exhibition showcasing energy-saving products, services, and technologies, with 44 companies participating. Furthermore, following FY2023, we continued in FY2024 to use the CDP*22 Supply Chain Program to better understand our suppliers’ initiatives, as well as related risks and opportunities.
In FY2025 and beyond, we will continue to collaborate with our business partners to promote activities aimed at reducing CO2 emissions throughout the supply chain.
- An international environmental NGO that collects requests from institutional investors and others interested in environmental issues, and encourages major companies and organizations around the world to disclose environmental information, and evaluate